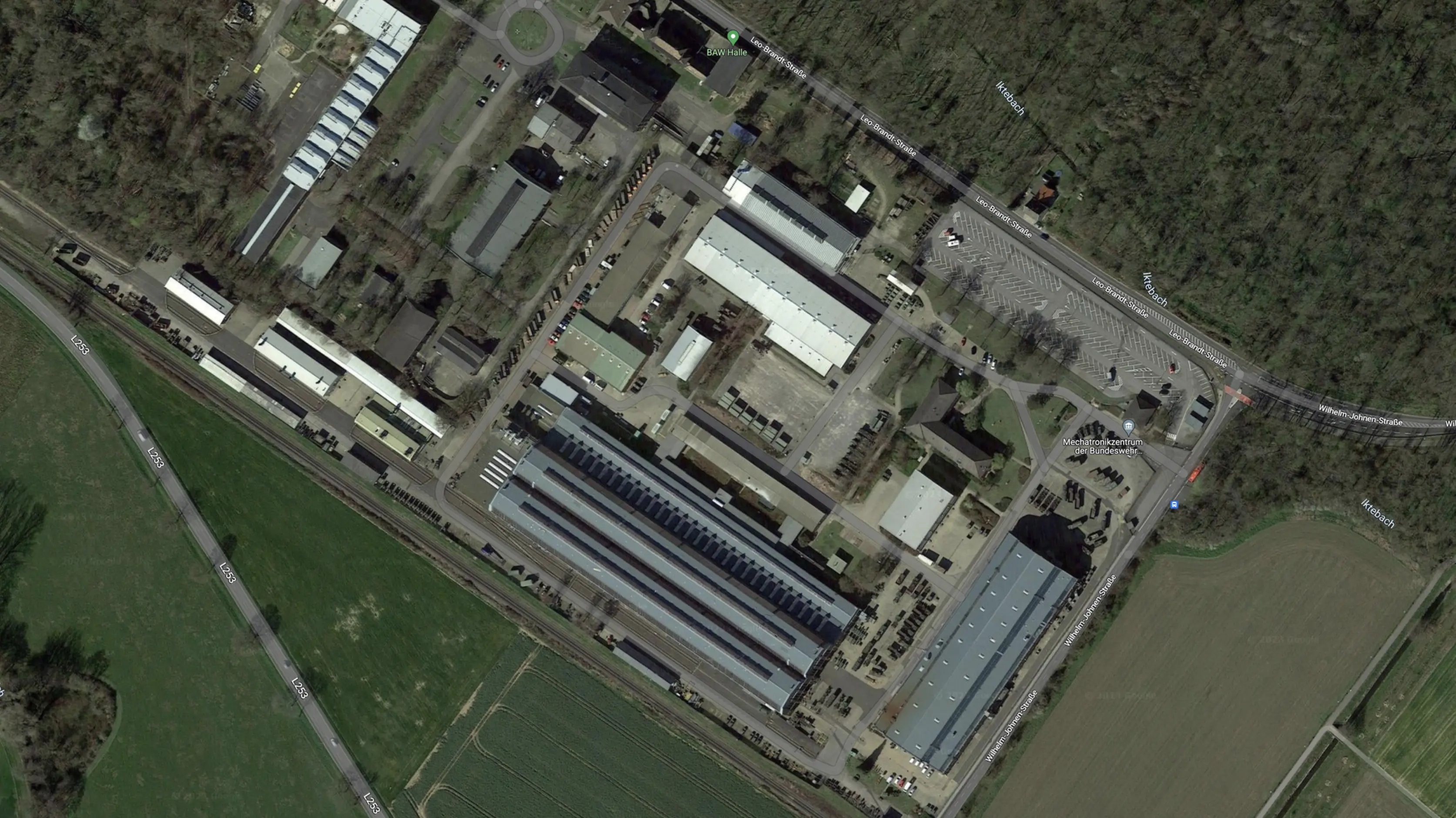
Streamlining Armored Vehicle Overhauls
Optimizing Maintenance Logistics for Maximum Readiness
The Mechatronics Center in Jülich processes and services armored vehicles that live a hard live being used in deployments across the world. When they come to the Mechatronics Center after years of service, vehicles are typically pretty banged up.
The mechanics in Jülich start the process of fully refurbishing them. This is a process that can take months. The vehicles are taken apart. All the parts are inspected and distributed to specialized work areas across the faciltiy for refurbishing - or if necessary replaced. Once all the parts are ready, the vehicle is re-assembled, given a fresh paint, and is driven outside for transport.
While this process unfolds, the parts are distributed across the vast premises spanning more than 13 football fields. Keeping track of which parts fit together is key. Ideally, the same parts go back to the same place in the same vehicle.
Revolutionizing army vehicle repair logistics
Report by the Cyber Innovation Hub of the Bundeswehr
The Cyber Innovation Hub said the following about our joint solution:
This means that the mechanics know immediately where the individual components are located and can share this knowledge with colleagues. This has greatly increased productivity in the plant. Dead times within processes are digitally visible thanks to the position data.
And not only the mechanics involved, but also the management benefits from tracking the assemblies. This is because the solution also increases the transparency of processing times, allowing potential for improvement to be identified.
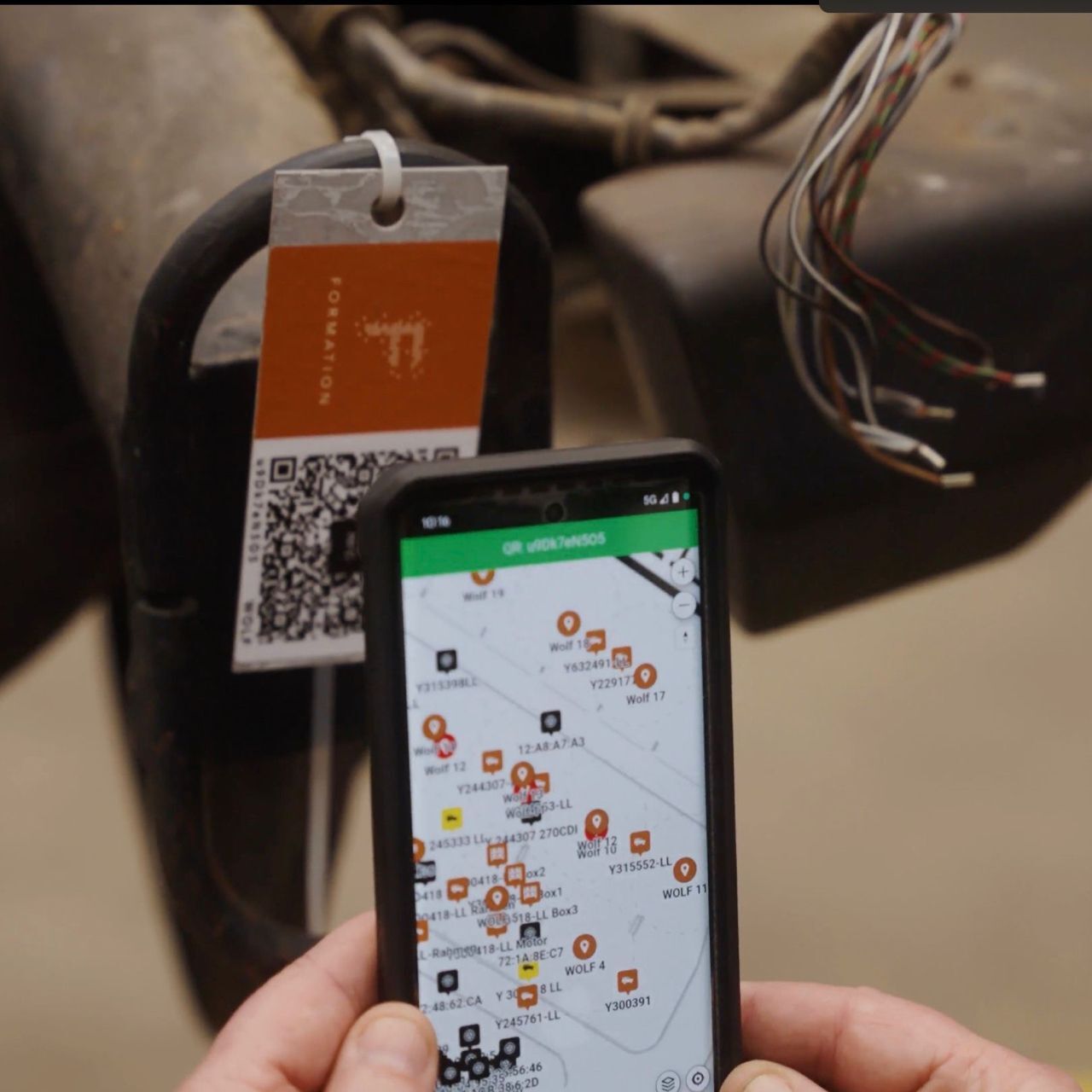
Hybrid Tracking drives the Process
Keeping track of everything
The hybrid tracking setup we deployed in Jülich uses both our QR Code Tags based solution and a BLE beacons from our partner Cavea. The beacons work in several of the halls where wireless anchors have been installed; outside those halls, people can update the location with their phone. Everytime a part or vehicle moves, location is updated on the FORMATION map.
.. heatmaps and path analyses provided valuable insights for further optimization of workflows and space utilization.
Cavea on the values delivered by FORMATION in this joint project
Mechanics can easily access the part details in FORMATION anywhere by scanning the QR Code Tag or by searching for it. When they do so, they can update the location, edit meta data, attach photos, and create follow up tasks .
Hybrid tracking works anywhere in the facility, and even off-premises and means that even parts that are stored outside the BLE covered halls are not lost.
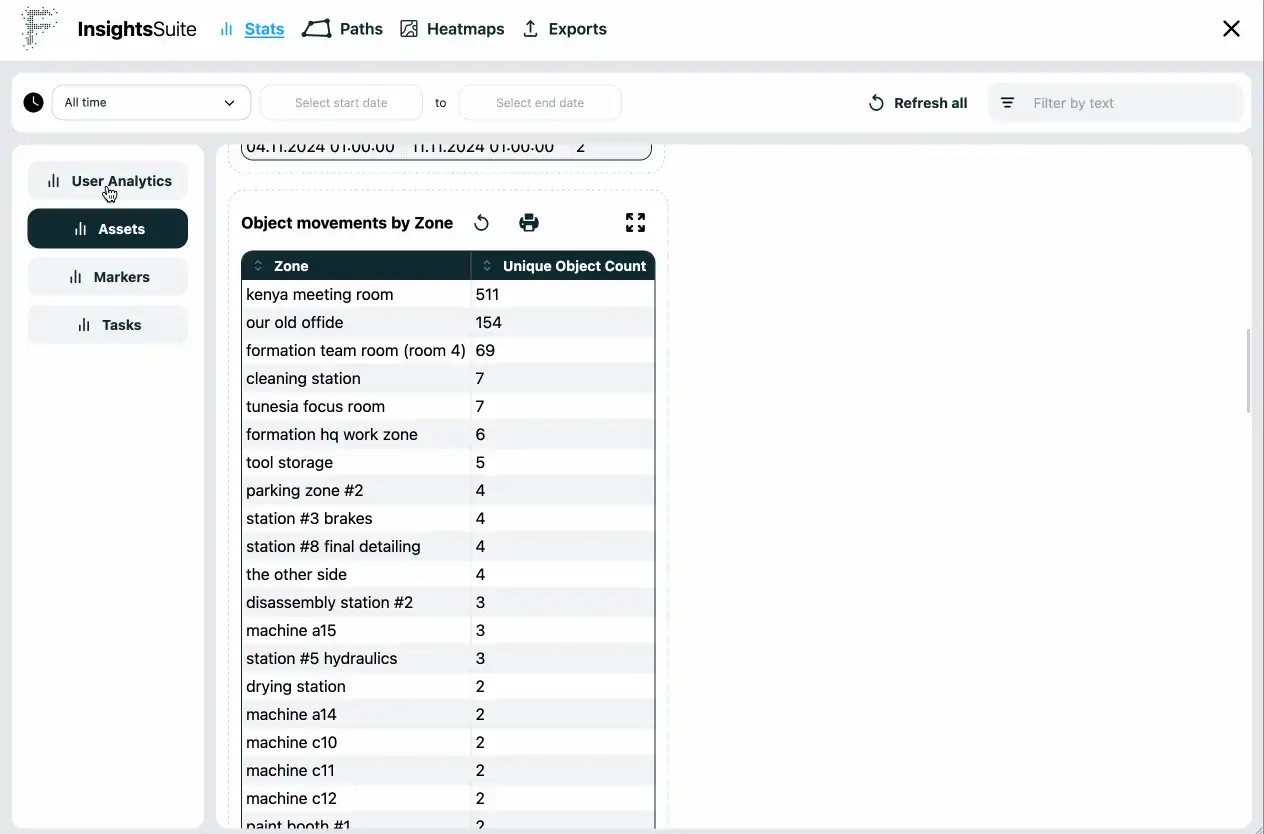
Keep the overview with Insights
React to issues, optimize processes, stay on top of targets.
The Insights Suite builds on the Hybrid Tracking. Insights provide situational awareness and make raw tracking data actionable to key decision makers of all ranks.
Whenever vehicles or parts leave or enter work zones in the Mechatronics Center, FORMATION stores this event. Over time this paints a picture of what happened when and where. The work process becomes visible from this data. We call this Emergent Process.
The Insights Suite provides several tools to slice and dice the raw data
- The paths tool shows movements between work zones.
- The history tool gives an auditing record of all movements between zones and when they happened.
- The heatmap tool provides an overview of large concentration of movements that indicate bottlenecks.
- The dashboard provides an overview of all the vehicles and parts and their current state.
- Export the data for use in spreadsheets and third party business analytics tools.
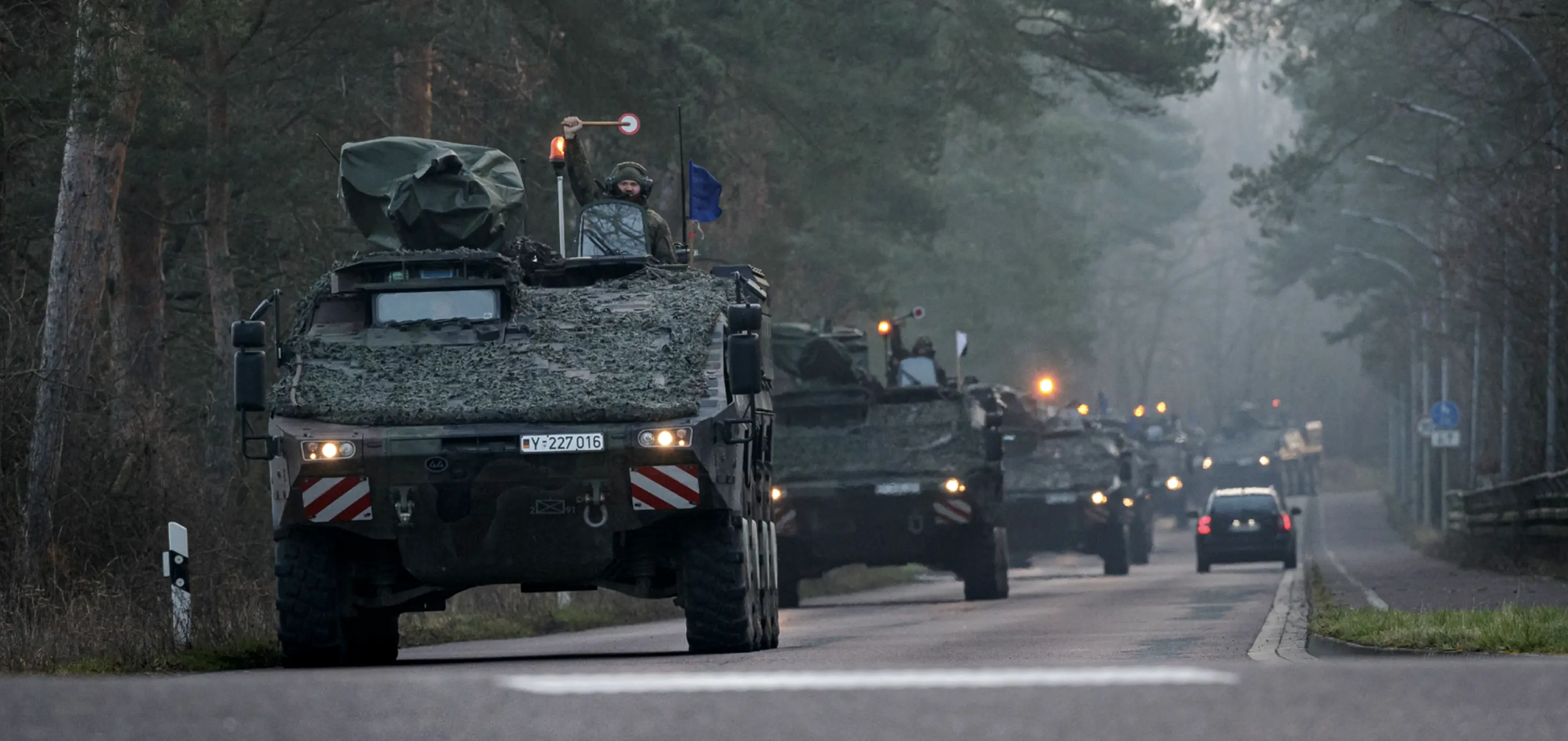
Strategic Deployment Planning
Leverage Spatial Intelligence
In 2024, in collaboration with the Cyber Innovation Hub, we developed a digital planning tool based on FORMATION. This system streamlines rapid deployment of field command nodes by integrating a geo-referenced digital map with a comprehensive library of tactical assets. It enables precise asset allocation and execution of operational orders, allowing commanders to establish command and control centers with enhanced situational awareness.
By replacing older mapping methods, the tool minimizes on-the-fly changes and expedites setup in the field. Currently, the solution we’ve built for the Army is under evaluation, and we hope to report on the findings soon.
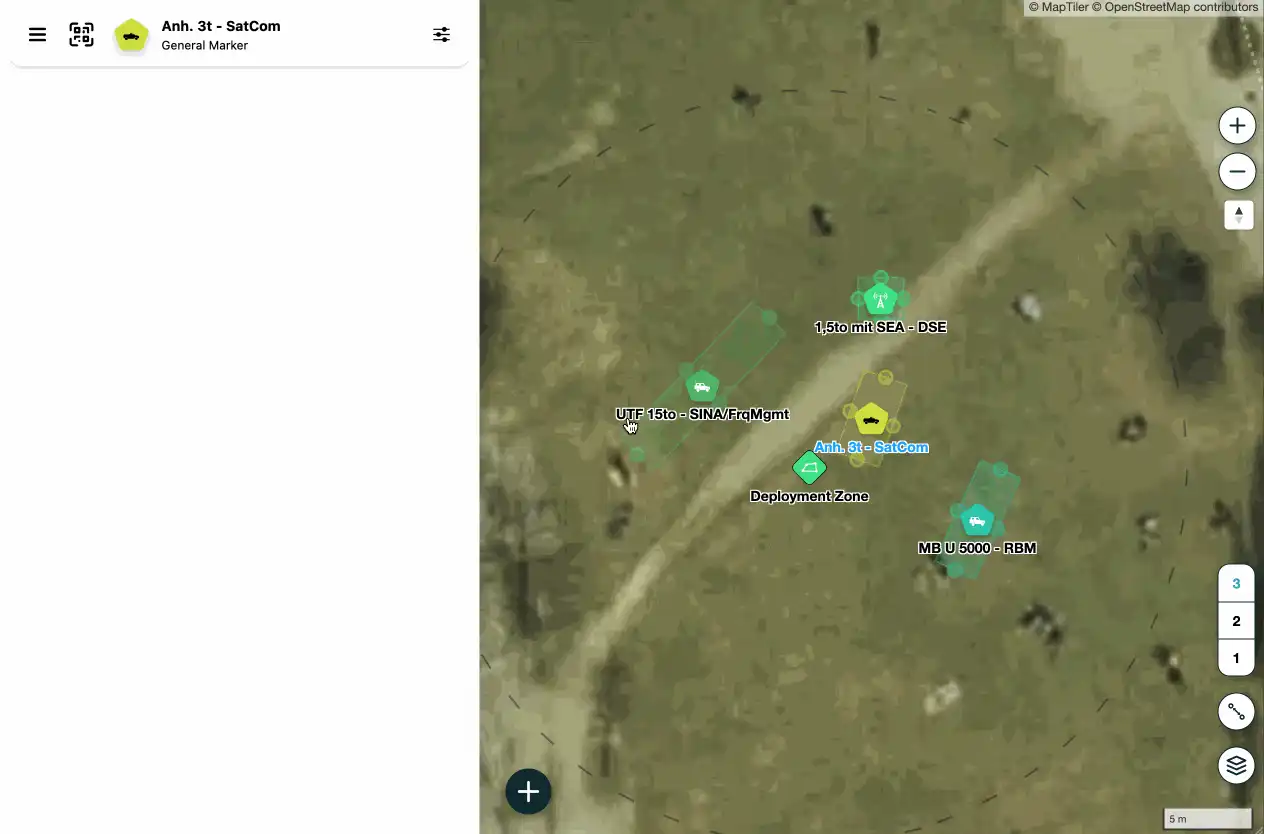
Optimized Deployment of Command Nodes
Enhancing Efficiency in Tactical Operations
With FORMATION, deployment sites are planned using a digital mission planning tool that integrates a digital map with up-to-date satellite imagery and a library of assets ready for placement. The system use global geospatial intelligence and dual-mode GPS and UTM coordinate search. This achieves precise asset positioning across the area of operations.
This streamlined planning process minimizes operational delays and enhances mission readiness, benefiting tactical operators, command elements as well as ground units.
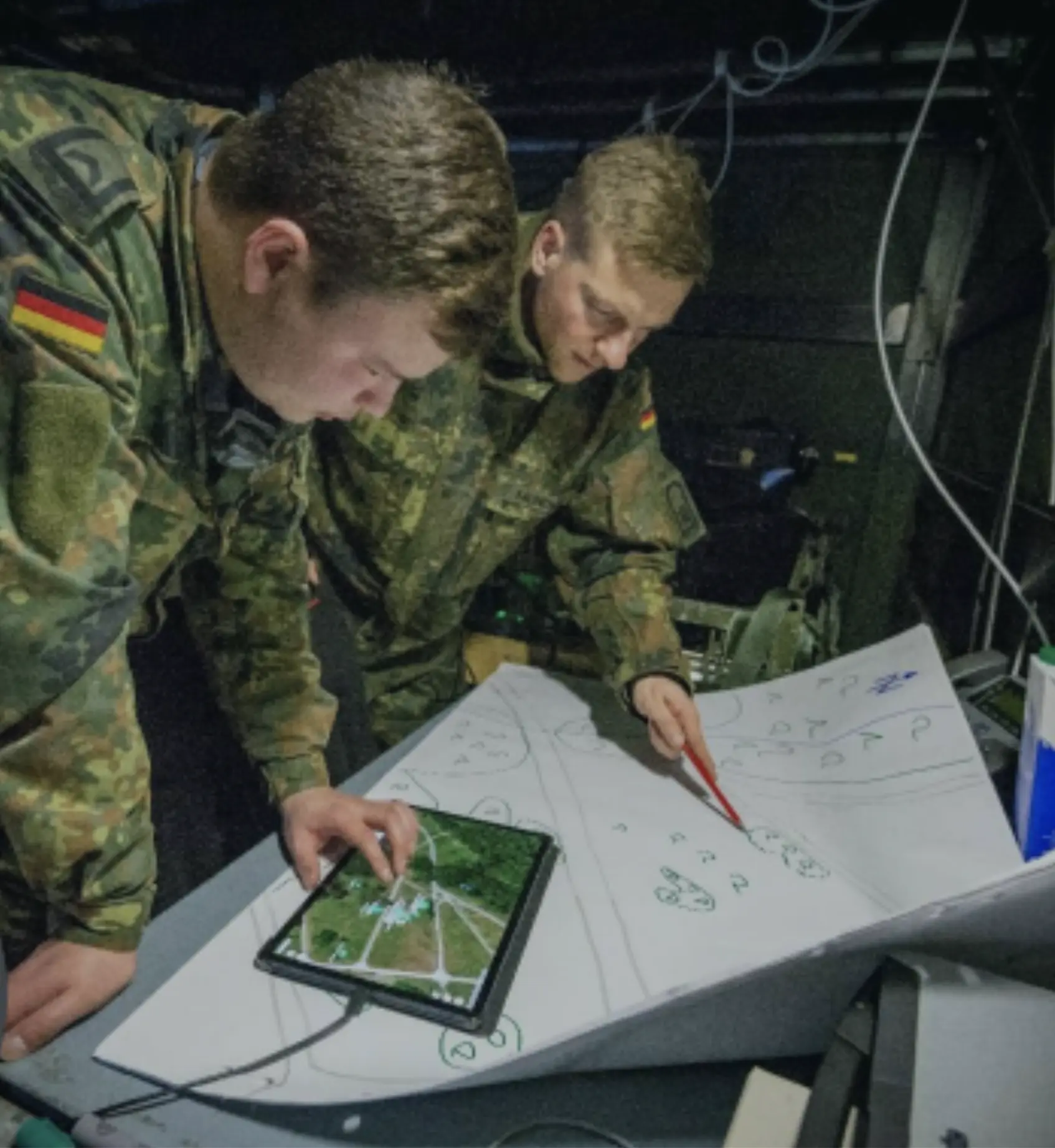
Tactical Advantages of FORMATION
Rapid Planning - Adapt dynamically to battlefield changes.
The deployment planning tool significantly reduces reconnaissance time and improves the success rate of map-based planning. Allowing in particular for:
- Faster planning phase
- Less errors during planning phase
- Mobile field execution plans
- Faster field execution in practice
- Less errors during field execution